The American Society of Mechanical Engineers (ASME) Section VIII outlines the rules for the construction of pressure vessels. These guidelines are crucial for ensuring the safety, design, fabrication, testing, and certification of pressure vessels used in various industries, such as chemical, petroleum, and power generation. Preparing for an interview related to ASME Section VIII can be daunting due to the technical complexity and extensive knowledge required. This cheat sheet aims to provide you with 50+ key questions and answers to help you ace your interview on Pressure Vessel – ASME Section VIII.
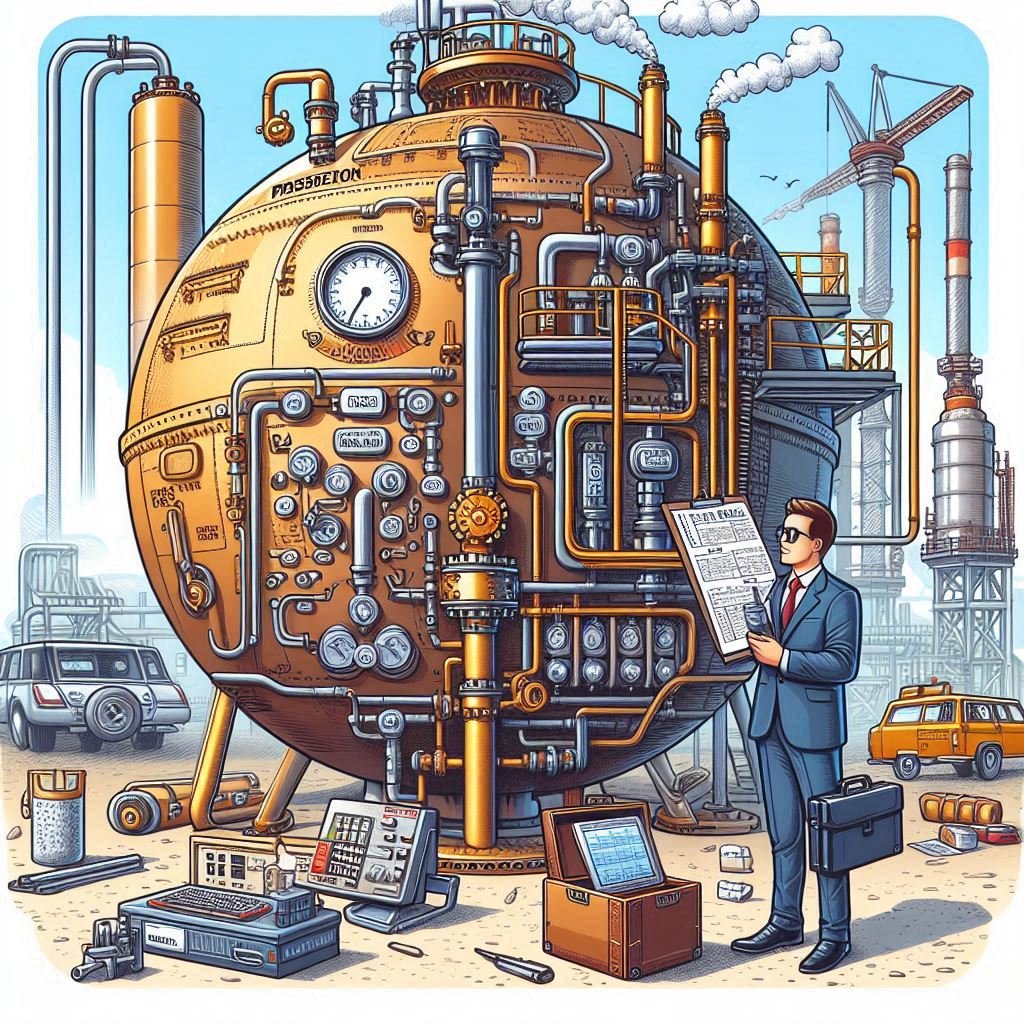
Pressure Vessel – ASME Section VIII Interview Cheat Sheet
- Q: What is ASME Section VIII?
A: ASME Section VIII is a part of the ASME Boiler and Pressure Vessel Code (BPVC) that provides requirements for the design, fabrication, inspection, testing, and certification of pressure vessels. - Q: What are the divisions of ASME Section VIII?
A: ASME Section VIII is divided into three divisions: Division 1 (Rules for Construction of Pressure Vessels), Division 2 (Alternative Rules – Pressure Vessels), and Division 3 (Alternative Rules for Construction of High Pressure Vessels). - Q: What is the main difference between Division 1 and Division 2 of ASME Section VIII?
A: Division 1 provides general rules for the construction of pressure vessels and is less stringent, while Division 2 provides alternative rules with more detailed stress analysis and higher safety factors for more critical applications. - Q: What materials are commonly used in the construction of pressure vessels according to ASME Section VIII?
A: Common materials include carbon steel, stainless steel, alloy steel, and non-ferrous materials such as aluminum and copper alloys. - Q: What is the purpose of a pressure relief device in a pressure vessel?
A: Pressure relief devices are used to protect the pressure vessel from overpressure conditions by relieving excess pressure. - Q: How is the Maximum Allowable Working Pressure (MAWP) determined?
A: MAWP is determined based on the weakest component of the vessel, considering factors such as material strength, temperature, and thickness. - Q: What is the significance of the Joint Efficiency (E) in pressure vessel design?
A: Joint Efficiency accounts for the strength reduction due to welded joints and is used in the calculation of the vessel’s thickness and MAWP. - Q: What are the types of welds commonly used in pressure vessel fabrication?
A: Common weld types include butt welds, fillet welds, and full penetration welds. - Q: Explain the concept of hydrostatic testing.
A: Hydrostatic testing involves filling the vessel with water and pressurizing it to a specified level to check for leaks and structural integrity. - Q: What is a stress concentration factor, and why is it important?
A: Stress concentration factors account for increased stresses around geometric discontinuities and are crucial for accurate stress analysis. - Q: What is the role of a certified pressure vessel inspector?
A: A certified inspector ensures that the pressure vessel complies with ASME standards through inspection and verification of design, materials, fabrication, and testing. - Q: Describe the process of Non-Destructive Testing (NDT) in pressure vessel inspection.
A: NDT methods such as radiography, ultrasonic testing, magnetic particle testing, and dye penetrant testing are used to detect defects without damaging the vessel. - Q: What is the importance of the Charpy impact test in pressure vessel materials?
A: The Charpy impact test measures the material’s toughness and its ability to absorb energy during fracture, which is critical for evaluating performance under sudden loading conditions. - Q: How does ASME Section VIII address corrosion allowance?
A: ASME Section VIII requires adding extra thickness to the vessel’s walls to account for expected material loss due to corrosion over its service life. - Q: What are the requirements for pressure vessel nameplates according to ASME Section VIII?
A: Nameplates must include information such as the manufacturer’s name, vessel serial number, MAWP, test pressure, and material specifications. - Q: What is the significance of the fatigue analysis in pressure vessel design?
A: Fatigue analysis evaluates the vessel’s ability to withstand cyclic loading and prevent fatigue failure over its service life. - Q: Explain the term “heat treatment” in the context of pressure vessel fabrication.
A: Heat treatment processes, such as annealing and stress relieving, are used to enhance material properties and relieve residual stresses from welding and forming. - Q: What is a nozzle in a pressure vessel, and what are its types?
A: A nozzle is an opening for inlet/outlet connections, instrumentation, or inspection. Types include radial, tangential, and offset nozzles. - Q: What is the role of design pressure in pressure vessel design?
A: Design pressure is the maximum internal pressure the vessel is designed to withstand during operation, and it serves as the basis for calculating vessel thickness and MAWP. - Q: How is the thickness of a pressure vessel shell calculated?
A: The thickness is calculated based on internal pressure, material strength, joint efficiency, and corrosion allowance using formulas specified in ASME Section VIII. - Q: What are the requirements for welding procedures in pressure vessel fabrication?
A: Welding procedures must be qualified according to ASME Section IX, ensuring they produce sound and reliable welds. - Q: Describe the importance of post-weld heat treatment (PWHT).
A: PWHT is performed to reduce residual stresses, improve material toughness, and enhance the metallurgical properties of welds. - Q: What is the difference between internal and external pressure in the context of pressure vessels? A: Internal pressure refers to the pressure exerted from within the vessel, while external pressure is applied from outside the vessel, often relevant in vacuum conditions.
- Q: What are the inspection requirements for pressure vessels during fabrication?
A: Inspections include material verification, dimensional checks, weld quality, NDT, hydrostatic testing, and final visual inspection to ensure compliance with ASME standards. - Q: How does ASME Section VIII address the use of bolts and flanges in pressure vessel construction? A: It provides guidelines for selecting bolt materials, calculating bolt loads, and ensuring flange design meets pressure and temperature requirements.
- Q: What is the significance of a pressure vessel’s design temperature?
A: Design temperature is the maximum temperature the vessel is designed to withstand during operation, affecting material selection and thickness calculations. - Q: Explain the term “joint efficiency” in the context of pressure vessel welding.
A: Joint efficiency represents the quality of a welded joint relative to the base material, impacting the overall strength and allowable stress of the vessel. - Q: What are the requirements for material traceability in pressure vessel construction?
A: Material traceability ensures that all materials used in construction can be traced back to their origin, including material certifications and heat treatment records. - Q: How does ASME Section VIII address the design of pressure vessel supports?
A: It provides guidelines for designing supports to ensure stability, load distribution, and resistance to seismic and wind forces. - Q: What is the purpose of a pressure vessel’s manway?
A: A manway is an access opening used for inspection, maintenance, and cleaning of the interior of the pressure vessel. - Q: Describe the process of a pressure vessel’s design approval according to ASME Section VIII.
A: Design approval involves reviewing design calculations, drawings, and specifications to ensure compliance with ASME standards before fabrication begins. - Q: What are the common types of pressure vessels?
A: Common types include storage tanks, heat exchangers, reactors, and autoclaves, each designed for specific applications and operating conditions. - Q: How does ASME Section VIII address the use of non-metallic materials in pressure vessels?
A: It provides guidelines for using non-metallic materials, such as composites and plastics, ensuring they meet the required mechanical properties and compatibility with the contained fluid. - Q: What is the importance of a pressure vessel’s internal coating?
A: Internal coatings protect the vessel from corrosion, chemical attack, and contamination of the contained fluid. - Q: Explain the term “allowable stress” in pressure vessel design.
A: Allowable stress is the maximum stress a material can safely withstand under specific conditions, used in design calculations to ensure structural integrity. - Q: What is the role of the ASME Authorized Inspector in pressure vessel construction?
A: The ASME Authorized Inspector verifies that the pressure vessel is built according to ASME standards through inspection, testing, and documentation review. - Q: How does ASME Section VIII address pressure vessel repairs and alterations?
A: It provides guidelines for evaluating, planning, and executing repairs and alterations to ensure the vessel remains safe and compliant with standards. - Q: What is the significance of the fatigue life of a pressure vessel?
A: Fatigue life refers to the number of cycles a pressure vessel can withstand before failure, critical for vessels subject to cyclic loading. - Q: Describe the importance of pressure vessel certification.
A: Certification ensures that the pressure vessel meets all ASME requirements for design, fabrication, inspection, and testing, providing assurance of safety and reliability. - Q: What is the purpose of the Pressure Vessel User’s Design Specification (UDS)?
A: The UDS provides detailed information about the pressure vessel’s intended use, operating conditions, and design requirements, guiding the design and fabrication process. - Q: Explain the term “minimum design metal temperature” (MDMT).
A: MDMT is the lowest temperature at which the pressure vessel can safely operate, considering material properties and fracture toughness. - Q: How does ASME Section VIII address the use of reinforcement pads?
A: Reinforcement pads are used to strengthen areas around openings, such as nozzles and manways, ensuring structural integrity under pressure. - Q: What is the role of Finite Element Analysis (FEA) in pressure vessel design?
A: FEA is used to perform detailed stress analysis, identify critical areas, and optimize the design for safety and performance. - Q: Describe the process of pressure vessel commissioning.
A: Commissioning involves preparing the vessel for operation, including cleaning, inspection, testing, and verifying compliance with design specifications. - Q: How does ASME Section VIII address the use of thermal expansion joints?
A: Thermal expansion joints accommodate thermal growth and contraction, preventing excessive stresses in the pressure vessel. - Q: What are the requirements for pressure vessel documentation?
A: Documentation includes design calculations, material certificates, welding procedures, inspection reports, and test records, ensuring traceability and compliance. - Q: Explain the concept of pressure vessel overpressure protection.
A: Overpressure protection involves using safety devices, such as relief valves and rupture discs, to prevent the vessel from exceeding its MAWP. - Q: How does ASME Section VIII address the design of pressure vessels for hazardous materials?
A: It provides guidelines for material selection, design considerations, and safety measures to ensure the containment of hazardous materials. - Q: What is the significance of the ASME “U” stamp?
A: The “U” stamp indicates that the pressure vessel has been manufactured and inspected according to ASME Section VIII requirements, certifying its compliance. - Q: How does ASME Section VIII address the use of pressure vessel insulation?
A: Insulation is used to maintain temperature, reduce heat loss, and protect personnel from hot surfaces, with guidelines for material selection and installation. - Q: What is the purpose of a pressure vessel’s nameplate data?
A: The nameplate provides essential information about the pressure vessel, including design and operating parameters, material specifications, and manufacturer details. - Q: Describe the importance of the pressure vessel’s design life.
A: Design life is the expected operational lifespan of the pressure vessel, considering factors such as fatigue, corrosion, and wear. - Q: How does ASME Section VIII address the use of safety factors in design?
A: Safety factors account for uncertainties in material properties, loading conditions, and fabrication quality, ensuring a margin of safety in the vessel’s design. - Q: What are the inspection intervals for pressure vessels according to ASME Section VIII?
A: Inspection intervals depend on the vessel’s service conditions, risk assessment, and regulatory requirements, ensuring ongoing safety and integrity. - Q: Explain the term “pressure vessel internals” and their significance.
A: Internals include components such as baffles, trays, and heat exchangers, essential for the vessel’s functionality and performance in specific applications.
This cheat sheet provides a comprehensive overview of key questions and answers related to ASME Section VIII. By understanding these concepts, you can confidently approach your interview and demonstrate your knowledge of pressure vessel design, fabrication, and inspection according to ASME standards.
You can also find some good books on general interview questions for Mechanical Engineers here.
You can also visit blog on 50+ most important questions on Pressure Vessels by clicking here.