Introduction to Basic of ASME Section VIII – Pressure Vessels:
Understanding the fundamentals of ASME Section VIII – Pressure Vessels is crucial for engineering professionals involved in the design, fabrication, and inspection of these critical components. ASME Section VIII provides comprehensive guidelines and standards to ensure the safety, reliability, and performance of pressure vessels under various operating conditions. This blog presents a collection of essential interview questions and answers focused on the basics of ASME Section VIII – Pressure Vessels, helping you prepare effectively for your next engineering interview. Whether you’re a seasoned professional or new to the field, mastering these topics will enhance your knowledge and expertise in pressure vessel engineering.
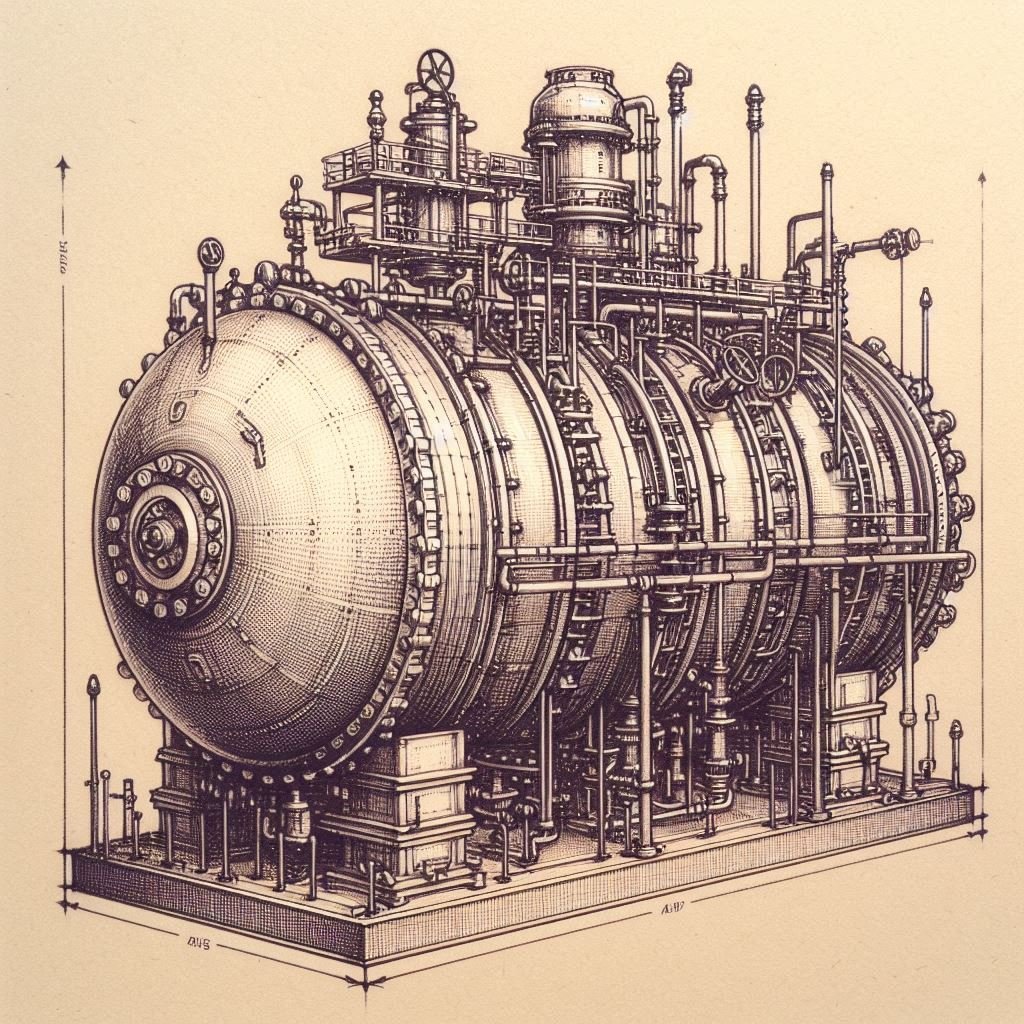
1. What is ASME Section VIII?
Answer: ASME Section VIII is a section of the ASME Boiler and Pressure Vessel Code (BPVC) that provides rules for the design, fabrication, testing, and inspection of pressure vessels. This section ensures that pressure vessels are safe and reliable under the operating conditions they are designed for.
2. What are the three divisions of ASME Section VIII?
Answer: ASME Section VIII is divided into three divisions:
- Division 1: Covers pressure vessels operating at pressures not exceeding 3,000 psi. It provides detailed requirements for the design, fabrication, inspection, and testing.
- Division 2: Also known as the “Alternative Rules,” it allows for higher stress levels and requires a more rigorous analysis and testing process.
- Division 3: Covers pressure vessels operating at pressures above 10,000 psi, focusing on high-pressure applications.
3. Explain the importance of design by rule and design by analysis in ASME Section VIII.
Answer:
- Design by Rule: Commonly used in Division 1, it involves using standard formulas and criteria provided by the code for designing pressure vessels. It is simpler and widely used for typical applications.
- Design by Analysis: Emphasized in Division 2, it requires a detailed stress analysis and a more thorough understanding of the vessel’s behavior under different loading conditions. This method is used for more complex and high-stress vessels.
4. What is a pressure vessel and why is it important to follow ASME Section VIII for its construction?
Answer: A pressure vessel is a container designed to hold gases or liquids at a pressure substantially different from the ambient pressure. Following ASME Section VIII is important because it provides standardized guidelines ensuring that the pressure vessels are built to withstand the pressure and temperature conditions they will encounter, minimizing the risk of accidents and failures.
5. Describe the role of the Material Selection in ASME Section VIII.
Answer: Material selection is crucial in ASME Section VIII because the materials must be able to withstand the pressure, temperature, and corrosive conditions they will encounter. The code provides specifications for materials that are suitable for use in pressure vessels, ensuring their mechanical properties are adequate for safe operation.
6. What are the typical steps involved in the fabrication of a pressure vessel according to ASME Section VIII?
Answer: The typical steps include:
- Design: Following the code’s rules and conducting necessary analyses.
- Material Selection: Choosing materials that meet the code’s specifications.
- Fabrication: Using approved methods and techniques for forming and welding.
- Inspection and Testing: Performing non-destructive testing, hydrostatic testing, and other inspections to ensure the vessel meets the code’s requirements.
- Documentation: Maintaining detailed records of the design, fabrication, inspection, and testing processes.
7. Explain the significance of the term “MAWP” in ASME Section VIII.
Answer: Maximum Allowable Working Pressure (MAWP) is the maximum pressure that a pressure vessel can safely withstand during its operation at a specified temperature. It is determined based on the design calculations and the material’s strength, considering the most severe conditions that the vessel is expected to encounter.
8. What are some common types of non-destructive testing (NDT) methods used in the inspection of pressure vessels?
Answer: Common NDT methods include:
- Radiographic Testing (RT): Uses X-rays or gamma rays to examine the internal structure.
- Ultrasonic Testing (UT): Uses high-frequency sound waves to detect flaws.
- Magnetic Particle Testing (MT): Detects surface and near-surface defects in ferromagnetic materials.
- Liquid Penetrant Testing (PT): Uses a dye to detect surface cracks and flaws.
- Visual Inspection (VT): The simplest method, involving careful visual examination of the vessel’s surface.
9. How does ASME Section VIII address the issue of corrosion allowance?
Answer: ASME Section VIII requires designers to account for potential corrosion during the vessel’s operational life by adding a corrosion allowance to the thickness of the vessel walls. This ensures that even with material loss due to corrosion, the vessel remains safe and functional.
10. What is the purpose of a hydrostatic test in the context of ASME Section VIII?
Answer: A hydrostatic test is performed to verify the structural integrity and leak-tightness of a pressure vessel. The vessel is filled with water and pressurized to a level higher than its MAWP to ensure it can handle its intended operating conditions without leaking or failing.
2/2
4o
WRITE DOWN ANOTHER 30ChatGPT
Sure! Here are 30 more interview questions and answers related to the basics of ASME Section VIII:
11. What is the difference between MAWP and Design Pressure?
Answer: The Maximum Allowable Working Pressure (MAWP) is the highest pressure that the pressure vessel can withstand safely under normal operating conditions. Design Pressure is the pressure used in the design calculations to ensure the vessel’s safety and is usually slightly higher than the MAWP to provide a safety margin.
12. What is a pressure relief device, and why is it important in pressure vessels?
Answer: A pressure relief device, such as a safety valve or rupture disc, is used to prevent overpressure conditions in a pressure vessel. It is crucial because it automatically releases pressure when it exceeds the MAWP, protecting the vessel from potential failure or explosion.
13. How is the corrosion allowance determined?
Answer: The corrosion allowance is determined based on the expected corrosion rate of the material in the operating environment over the vessel’s intended lifespan. This rate is typically derived from historical data, environmental conditions, and material properties.
14. Explain the term “joint efficiency” in welding.
Answer: Joint efficiency is a factor used in design calculations that reflects the strength of a welded joint relative to the strength of the base material. It accounts for imperfections and inconsistencies in the welding process and varies depending on the type of weld and the inspection method used.
15. What are the main considerations when selecting a material for a pressure vessel?
Answer: Main considerations include:
- Mechanical properties (strength, toughness, etc.)
- Corrosion resistance
- Operating temperature and pressure
- Compatibility with the contained fluid
- Cost and availability
16. Describe the purpose of a heat treatment process in pressure vessel fabrication.
Answer: Heat treatment processes, such as annealing, normalizing, and stress relieving, are used to enhance the mechanical properties of the material, relieve residual stresses, and improve the vessel’s structural integrity and toughness.
17. What is a “Code Stamp” in ASME Section VIII?
Answer: A Code Stamp (e.g., “U” stamp for pressure vessels) is a certification mark that indicates a pressure vessel has been designed, constructed, inspected, and tested in accordance with the requirements of ASME Section VIII. It signifies compliance with the ASME Code.
18. How is the thickness of a pressure vessel shell calculated?
Answer: The thickness is calculated using formulas provided in ASME Section VIII, considering the internal pressure, material strength, joint efficiency, and corrosion allowance. The formulas ensure the shell can withstand the operating conditions safely.
19. What is the significance of post-weld heat treatment (PWHT)?
Answer: PWHT reduces residual stresses induced by welding, enhances toughness, and improves the overall mechanical properties of the weld and the heat-affected zone. It is especially important for thick-walled vessels and high-stress applications.
20. What are the key differences between Division 1 and Division 2 of ASME Section VIII?
Answer:
- Division 1: Uses design-by-rule methods, is less complex, and applies to a broader range of standard pressure vessel applications.
- Division 2: Uses design-by-analysis methods, allows for higher stress levels, and requires more detailed design and testing, suitable for more critical and complex applications.
21. What is the purpose of a pressure test, and what are the common types?
Answer: A pressure test ensures the integrity and leak-tightness of a pressure vessel. Common types include:
- Hydrostatic Test: Uses water to pressurize the vessel.
- Pneumatic Test: Uses air or gas to pressurize the vessel, typically when water could cause contamination or damage.
22. Explain the concept of “double-walled” pressure vessels.
Answer: Double-walled pressure vessels have an inner and outer shell, often with insulation or a vacuum between them. This design improves thermal efficiency, safety, and containment of hazardous materials.
23. How does ASME Section VIII address fatigue analysis?
Answer: ASME Section VIII requires a fatigue analysis for pressure vessels subjected to cyclic loading. This analysis assesses the potential for fatigue failure over the vessel’s operational life, considering the number of cycles, stress ranges, and material properties.
24. What are the documentation requirements for pressure vessels under ASME Section VIII?
Answer: Documentation requirements include design calculations, material certifications, welding procedure specifications, inspection and test reports, and the Manufacturer’s Data Report. These records ensure traceability and compliance with the code.
25. What is a rupture disc, and how does it function?
Answer: A rupture disc is a non-reclosing pressure relief device designed to burst at a predetermined pressure, relieving excess pressure to protect the vessel from overpressure conditions. It provides a fail-safe mechanism in case of pressure buildup.
26. Describe the role of finite element analysis (FEA) in pressure vessel design.
Answer: FEA is a computational method used to analyze complex stress distributions in pressure vessels. It helps in identifying critical stress points, optimizing design, and ensuring the vessel can withstand operational loads, especially in Division 2 and Division 3 designs.
27. What is the purpose of impact testing in pressure vessel materials?
Answer: Impact testing evaluates a material’s toughness and its ability to absorb energy during a sudden impact. It is crucial for ensuring the material can withstand low-temperature conditions and resist brittle fracture.
28. Explain the term “stress concentration” and its significance in pressure vessel design.
Answer: Stress concentration refers to localized areas of high stress, typically around discontinuities such as holes, notches, or welds. It is significant because these areas are prone to failure, and designers must account for them to ensure the vessel’s integrity.
29. What are the common causes of pressure vessel failure?
Answer: Common causes include:
- Material defects or degradation (corrosion, embrittlement)
- Design flaws or incorrect calculations
- Welding defects or poor workmanship
- Overpressure conditions
- Fatigue due to cyclic loading
30. How does ASME Section VIII ensure the safety of pressure vessels used in cryogenic applications?
Answer: For cryogenic applications, ASME Section VIII specifies materials with adequate toughness at low temperatures, requires stringent testing for brittleness, and may involve special design considerations to handle thermal stresses and insulation requirements.
31. What is the difference between a safety valve and a relief valve?
Answer: A safety valve is designed to open quickly and fully when the set pressure is exceeded, typically used for steam or gas applications. A relief valve opens more gradually to relieve excess pressure, commonly used in liquid applications.
32. Describe the purpose of a vessel’s nameplate.
Answer: A vessel’s nameplate provides essential information such as the manufacturer’s name, design pressure, MAWP, temperature limits, material specifications, and the code stamp. It ensures traceability and compliance with ASME Section VIII requirements.
33. What is the importance of the hydrostatic test pressure being higher than the MAWP?
Answer: Testing at a pressure higher than the MAWP (usually 1.3 to 1.5 times higher) ensures the vessel can handle pressures above its normal operating conditions, providing a safety margin and verifying the vessel’s integrity.
34. How are welding procedures qualified under ASME Section VIII?
Answer: Welding procedures are qualified through the creation and testing of procedure qualification records (PQRs). These records document the results of mechanical tests (e.g., tensile, bend tests) performed on sample welds to ensure the procedure produces sound welds.
35. What is a “nozzle” in the context of pressure vessels?
Answer: A nozzle is an opening in a pressure vessel used for the inlet or outlet of fluids, attachment of instruments, or as an access point for inspection and maintenance. Proper design and reinforcement are essential to maintain vessel integrity.
36. Explain the term “heat-affected zone” (HAZ).
Answer: The heat-affected zone (HAZ) is the area of the base material that is altered by the heat of welding. It is crucial because the properties of the HAZ can affect the overall strength and performance of the weld.
37. What is the purpose of radiographic testing in pressure vessel inspection?
Answer: Radiographic testing (RT) uses X-rays or gamma rays to create images of the internal structure of welds and components, allowing inspectors to detect hidden flaws such as cracks, voids, or inclusions without damaging the vessel.
38. How does ASME Section VIII address the issue of thermal expansion in pressure vessels?
Answer: ASME Section VIII requires designers to account for thermal expansion by selecting materials with suitable thermal properties, incorporating expansion joints or flexible connections, and performing stress analysis to ensure the vessel can withstand thermal stresses.
39. What is a “closure” in a pressure vessel?
Answer: A closure is a removable or fixed component that seals an opening in a pressure vessel, such as a manway cover or end cap. Closures must be designed to withstand the vessel’s internal pressure and ensure leak-tightness.
40. Describe the purpose of a vessel’s internal and external coating.
Answer: Internal and external coatings protect the vessel from corrosion, chemical attack, and environmental damage. They extend the vessel’s lifespan and maintain its structural integrity by providing a barrier between the material and the corrosive environment.
41. What is the importance of stress relieving in pressure vessel fabrication?
Answer: Stress relieving reduces residual stresses induced by welding, machining, or forming. This process improves the vessel’s dimensional stability, reduces the risk of stress corrosion cracking, and enhances overall durability.
42. How does ASME Section VIII ensure the quality of welds in pressure vessels?
Answer: ASME Section VIII ensures weld quality through rigorous qualification of welding procedures, welders, and welding operators. It also mandates non-destructive testing (NDT) of welds, such as radiographic or ultrasonic testing, to detect flaws and ensure compliance.
43. What is the purpose of a “pressure rating” for fittings and flanges?
Answer: The pressure rating indicates the maximum pressure that fittings and flanges can safely handle at specific temperatures. It ensures compatibility and safety when these components are used in conjunction with pressure vessels.
44. Explain the concept of “allowable stress” in pressure vessel design.
Answer: Allowable stress is the maximum stress that a material can withstand under operating conditions without failure. It is determined based on material properties, safety factors, and design codes, ensuring the vessel’s safe operation.
45. How does ASME Section VIII address the issue of cyclic loading and fatigue?
Answer: ASME Section VIII requires a fatigue analysis for vessels subject to cyclic loading. This analysis considers the number of cycles, stress ranges, and material properties to predict the vessel’s fatigue life and ensure it can withstand repeated loading without failure.
46. What are the common inspection methods used for pressure vessels during fabrication and in-service?
Answer: Common inspection methods include:
- Visual Inspection (VT)
- Radiographic Testing (RT)
- Ultrasonic Testing (UT)
- Magnetic Particle Testing (MT)
- Liquid Penetrant Testing (PT)
- Hydrostatic and Pneumatic Testing
47. Describe the role of the Authorized Inspector in ASME Section VIII.
Answer: The Authorized Inspector ensures compliance with ASME Section VIII during the fabrication, testing, and inspection of pressure vessels. They review design documents, inspect materials and fabrication processes, witness tests, and verify documentation.
48. What is a “shell” in the context of a pressure vessel?
Answer: The shell is the primary cylindrical or spherical body of a pressure vessel that contains the internal pressure. It is designed to withstand the pressure and provides the main structural support for the vessel.
49. Explain the term “seamless” in relation to pressure vessel construction.
Answer: Seamless construction refers to a pressure vessel or component made without welded seams. Seamless vessels are typically manufactured by extrusion, forging, or other processes that produce a continuous, unbroken structure, reducing the risk of weld-related defects.
50. How is the internal pressure of a pressure vessel typically monitored?
Answer: Internal pressure is monitored using pressure gauges, transducers, or sensors connected to the vessel. These devices provide real-time pressure readings and can trigger alarms or safety systems if the pressure exceeds safe limits.
51. What are the considerations for designing a pressure vessel for high-temperature applications?
Answer: Considerations include selecting materials with suitable high-temperature strength and creep resistance, accounting for thermal expansion and stress, ensuring adequate insulation, and performing rigorous analysis to prevent thermal degradation.
52. What is the purpose of a pressure vessel’s insulation?
Answer: Insulation helps maintain the temperature of the vessel’s contents, reduces heat loss or gain, prevents condensation, and protects personnel from contact with hot or cold surfaces. It enhances energy efficiency and operational safety.
53. How does ASME Section VIII address the issue of brittle fracture?
Answer: ASME Section VIII requires materials to be tested for toughness, especially at low temperatures, to prevent brittle fracture. Impact testing (e.g., Charpy tests) is used to ensure materials can absorb energy and resist sudden failure.
54. What is the significance of “minimum design metal temperature” (MDMT)?
Answer: MDMT is the lowest temperature at which a pressure vessel can safely operate without the risk of brittle fracture. It ensures the material retains adequate toughness and prevents failure due to low-temperature embrittlement.
55. Explain the term “yield strength” and its importance in pressure vessel design.
Answer: Yield strength is the stress at which a material begins to deform plastically. It is important in pressure vessel design because it determines the maximum allowable stress and ensures the vessel can withstand operational pressures without permanent deformation.
56. What are the common types of pressure vessel heads, and what are their applications?
Answer: Common types of pressure vessel heads include:
- Ellipsoidal Heads: Efficient for high-pressure applications, providing uniform stress distribution.
- Hemispherical Heads: Strongest design, used for very high-pressure vessels.
- Torispherical Heads: Economical and widely used for moderate pressures.
- Flat Heads: Simple but limited to low-pressure applications due to higher stress concentrations.
57. Describe the role of the Manufacturer’s Data Report in ASME Section VIII.
Answer: The Manufacturer’s Data Report documents all relevant information about the pressure vessel, including design calculations, material specifications, fabrication processes, inspection results, and test reports. It ensures traceability and compliance with ASME Section VIII.
58. What is the significance of “normalized” material in pressure vessel fabrication?
Answer: Normalized material has been heat-treated to refine its grain structure and improve its mechanical properties, such as strength and toughness. Normalization reduces residual stresses and enhances the material’s performance in pressure vessel applications.
59. How does ASME Section VIII address the issue of external pressure on pressure vessels?
Answer: ASME Section VIII provides guidelines for designing vessels to withstand external pressure (e.g., vacuum conditions) by specifying requirements for wall thickness, stiffening rings, and other reinforcement methods to prevent collapse or buckling.
60. Explain the concept of “proof testing” in pressure vessel design.
Answer: Proof testing involves subjecting a pressure vessel to a pressure higher than its MAWP to verify its structural integrity and leak-tightness. This test ensures the vessel can safely operate under its designed pressure and provides a margin of safety.
You can also find some good books on general interview questions for Mechanical Engineers here.
You can also visit blog on 50+ most important questions on Pressure Vessels by clicking here.